Interview; Quality is always top of mind at CIRFOOD
Interview with our quality manager Jeroen Disseldorp about Zenya software
As a leading company in the food industry, CIRFOOD knows all too well how important it is to deliver consistent quality. With 144 locations, including in educational institutions and companies such as KPN, maintaining a clear overview is extremely important to quality manager Jeroen Disseldorp. He is happy to talk to us about how Zenya helps do this.
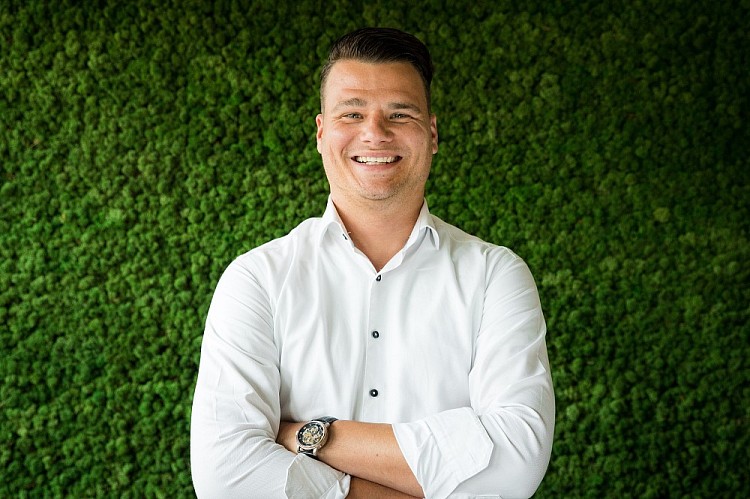
Zenya: a complete package that meets almost every need
“When I started at CIRFOOD a year and a half ago, my predecessor had already done quite a bit of preliminary work,”begins Jeroen. “He had made a shortlist of software packages that might meet the needs and requirements of our organisation.”“I was then completely free to make the choice”, he continues. “For me, the main thing was that the system made it easy for me to have an overview. Before we used Zenya, it wasn’t straightforward to create reports. That really had to change in my eyes, because good reporting is how you manage quality within an organisation like ours.”
The choice was made for Infoland’s Zenya software. “Zenya matches our requirements about 90-95%, which is just really nice”, says Jeroen. “If I had to pinpoint one thing that does not quite fit, it’s that the software can actually do more than we need right now. But who knows, in the future I might be thinking, ‘Great that it can also do that,’ so it’s certainly not a negative!”
Securing processes and workflows
CIRFOOD uses Zenya DOC to capture workflows and monitor standards such as ISO9001 and ISO14001. This program is mainly used at the head office. “We needed good document management for this, but also to be sure that not just anyone could make changes. Zenya DOC fits these requirements perfectly,” says Jeroen.
Zenya Flow is used for mapping recurring tasks and reporting incidents and discrepancies. The program is used by employees on-site for tasks such as ensuring temperature measurements are made on a regular basis within a workflow, but also for booking deliveries and reporting food safety incidents. All this helps to maintain compliance with HACCP standards.
“I wanted to be able to link a workflow to incident reporting, so that a report doesn’t always have to be dealt with immediately,” says Jeroen. “I get a signal from each report, so I can determine whether a follow-up is needed from here. We set that up in Zenya FLOW, and it works very well.”
Knowing what to do without having to think about it
“What is nice, for me and for the employees on site, is that all important, recurring tasks have been scheduled,” explains Jeroen. “Employees receive a notification that they need to do something, such as monitor the temperature. They can do it there and then and then continue their prior task immediately afterwards. If something is not done on time, they automatically get a reminder. So I no longer have to chase things up myself, unless tasks remain open for too long. The reports are not all set up quite the way I envisage yet, but trends are already visible. For instance, there are locations that often don’t do things until Friday afternoon and then they encounter discrepancies that can only be solved later. So I can start managing that.”
Jeroen is already noticing that employees have found their way around the mobile version of Zenya. “If they need to monitor the temperature, they go to Zenya on their own smartphone to record it on the spot,” he says. “Our FOODIES, external parties who offer their products at our locations, also work with Zenya and are making positive noises.”
Thanks to the positive reactions, Jeroen is now rolling out use of a tablet with the Zenya Capture App for each location. He can see benefits for the food branch in using the app for notifications and following up scheduled tasks. “We didn't actually plan on doing this until the end of 2022, but we were able to start working on it earlier as we have been mostly closed the past year and a half due to the coronavirus pandemic. A cloud with a silver lining.”
The future of quality management at CIRFOOD
Jeroen is still in the process of rolling out the Zenya Capture App, but the locations that are already using it are enthusiastic about it. “They find it really easy to use and, above all, they see that this way of working saves time,” he says. In addition, Jeroen is still setting up various reports. “A system like Zenya has to work for you, it shouldn’t become an administrative burden. Once I have a fully complete overview thanks to the reports, it will make my work so much easier. And then I can focus more on the real substance of my job, instead of peripheral administrative issues.”
While he is still optimising the use of the software, Jeroen is grateful to be able to call on the support of Infoland’s help desk. “I had an assistant,” he explains, “but unfortunately, given the situation, he couldn’t stay on. And I don't have the time and knowledge to do it all myself. So how good is it that I can call them and they help me out?”
Jeroen also sees a place for Infoland’s iQualify software for knowledge capture in the future. And he is interested in Zenya CHECK. “At the moment, we still use other software for audit management, but my goal is to bring that together with Zenya DOC and FLOW. It’s so convenient when everything is in one system. It also makes it much easier to demonstrate compliance with industry standards.”
It’s safe to say that Jeroen is happy with Zenya and that it helps him to secure and improve quality within CIRFOOD. Quality must be a priority throughout the organisation and is now always top of mind. He would like to see more organisations in the food industry working with Zenya, though: he says he sometimes feels a bit lonely on the Infoland community forum. But, more seriously, he sees above all how Zenya can help an organisation improve and maintain quality.
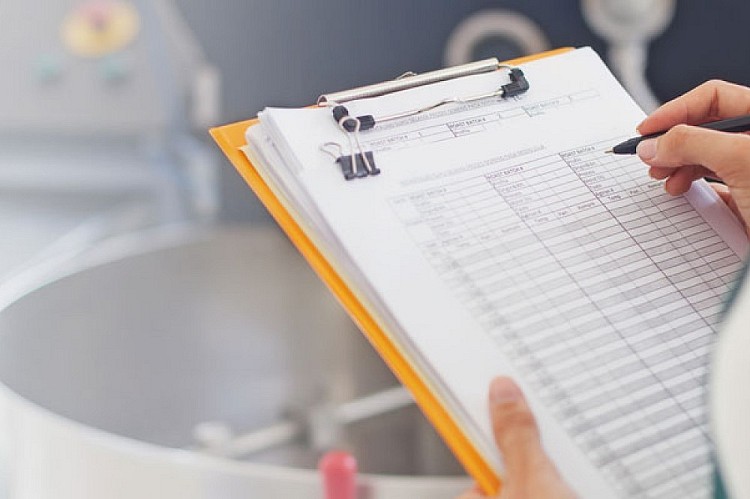